Roots

Leather town, Asakusa
Kadoya is one of the oldest leather jacket manufacturers in Japan. The corporate spirit of challenge and innovation has not wavered even after 85 years since its founding. Since its founding, Kadoya has put down roots in Asakusa and continues to operate.
Kadoya was founded in Asakusa in 1935, six years before the start of the Pacific War. The store name at the time of its founding was “Kadoya Leather Clothing Store,” a so-called clothing store. In Asakusa, a town of craftsmen, there were many similar clothing stores from those days.
Asakusa, Tokyo has long been home to many leather wholesalers, and many leather goods were made there.

founder
Shojiro Fukano
1935 (Showa 10)
Founder/Shojiro Fukano opens Kadoya Leather Clothing Store in Asakusa, Tokyo.
Taking advantage of the location of Asakusa, which is a mecca for the leather industry, the company handles repairs and dyeing of leather products, as well as tailoring leather clothing.
"Trust can only be earned by meeting customer needs."
The leather jackets made by Shojiro, who loves motorcycles, become popular, and soon a large number of riders with a passion for motorcycles are flocking to the jackets.
Kadoya's craftsmen, who have been making leather jackets for a long time as a made-to-order leather shop, have accumulated technology that can respond to all needs over time.
As the world entered an era of mass production and mass consumption, the trend shifted toward ready-made clothes.
In the midst of turbulent times, the skilled craftsmen led by Masataka Fukano, the second generation, started the development of ready-made clothes while continuing the conventional custom-made production.
In 2003, HEAD FACTORY, a purely domestic brand, went against the times and adhered to the style of "sewing one piece per person" as if it were going against the times. was launched at the factory in the head office building in Asakusa.
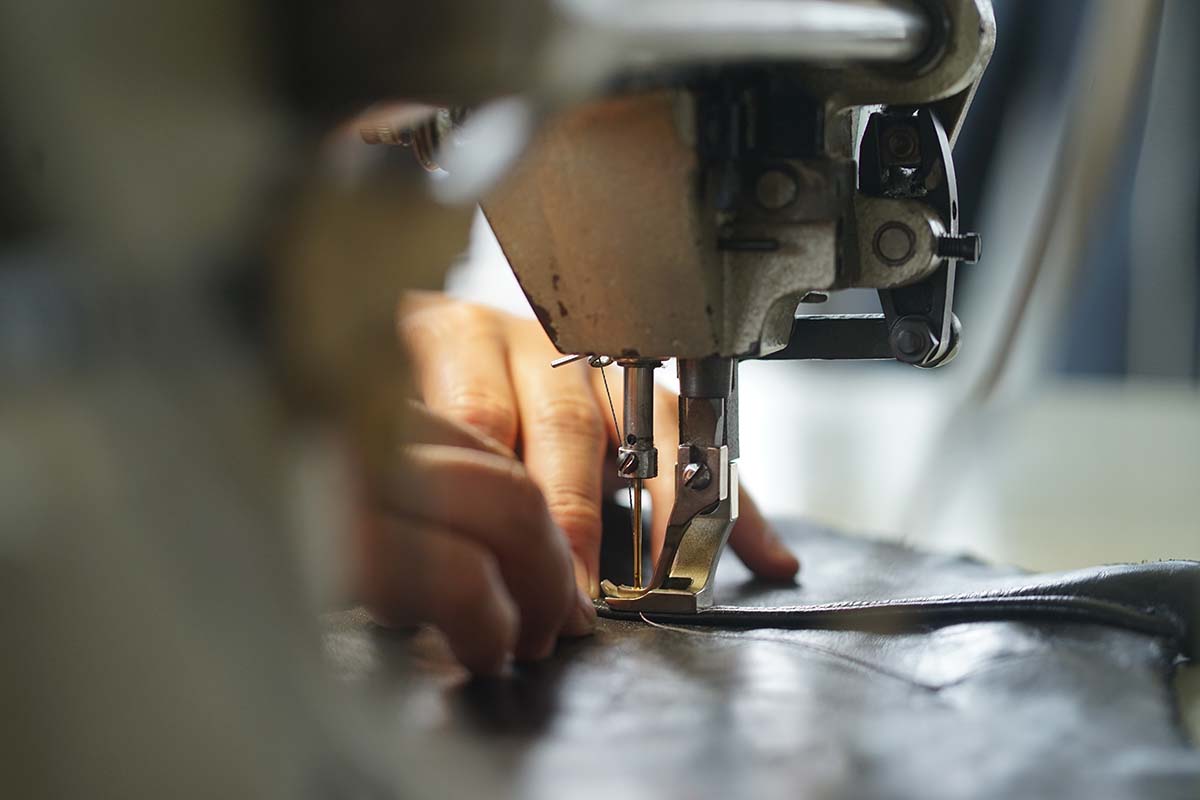
Subheading
technology and quality
When making functional clothes using a special material called leather, the essence resides even in the invisible parts.
Leather is a raw material, and each piece has a different character. You can't handle leather by relying on one-sided techniques.
The production method is constantly fine-tuned by identifying the individuality of the piece in front of you, making full use of the appropriate tools and techniques.
Diverse techniques and the spirit of awareness have been passed down from generation to generation to protect quality.

Subheading
to produce something better.
Manufacturing of custom-made products, production of ready-made products, and repair. The skills required for each of these three are different.
Head Factory products are then created from the center of this triangle.
The important things that come to light as we continue to respond to diverse needs are incorporated into the details of new products and transformed into a single jacket.
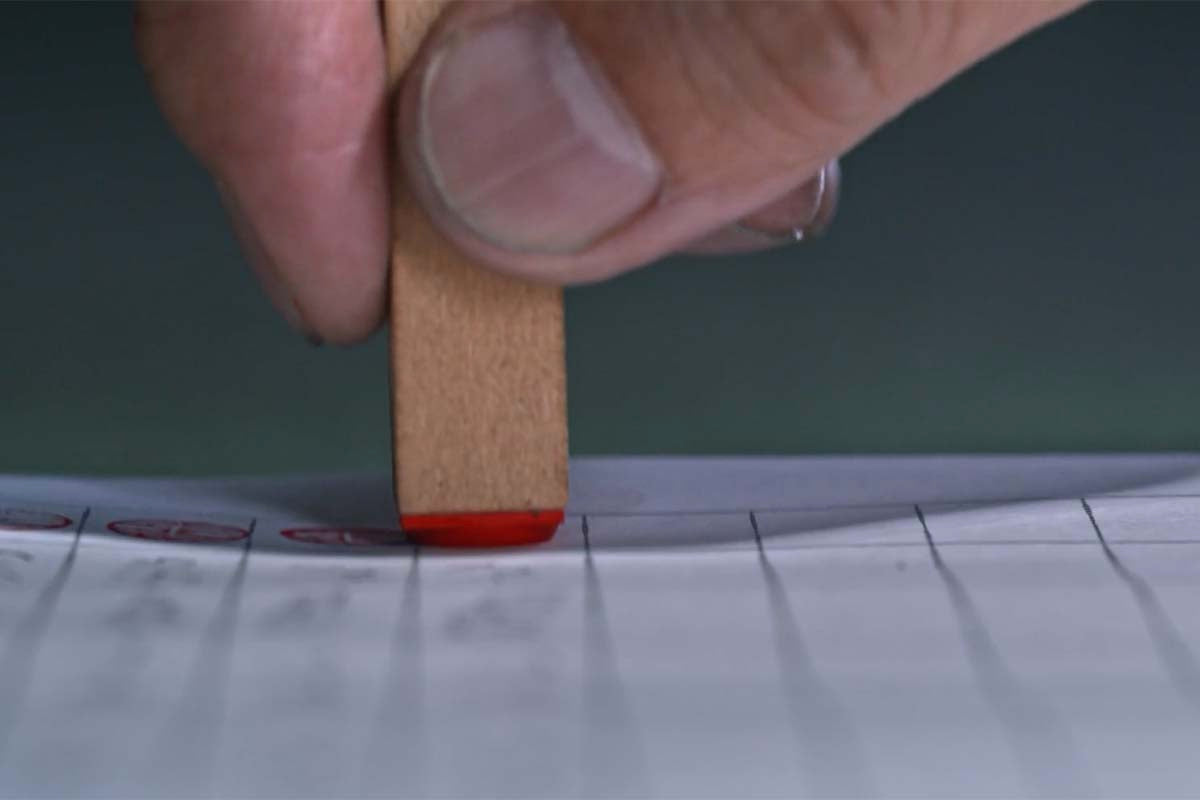
Subheading
Quality born from responsibility and pride
The stance of Head Factory, which has its origins in custom-made products, does not change even when it comes to making ready-made clothes. In other words, it is a style of "sewing one garment per person" in which one craftsman takes responsibility for each item.
When dealing with raw leather, a completely manual production system can lead to inconsistent quality as a result. The skillful adjustment of the craftsman who sews by himself is alive even in the production of ready-made products where individual differences are not allowed.
It goes without saying that there are no flaws in the manufacturing process, but after a rigorous and authentic assessment, we send it out with HEAD FACTORY pride.
About
Leather Material
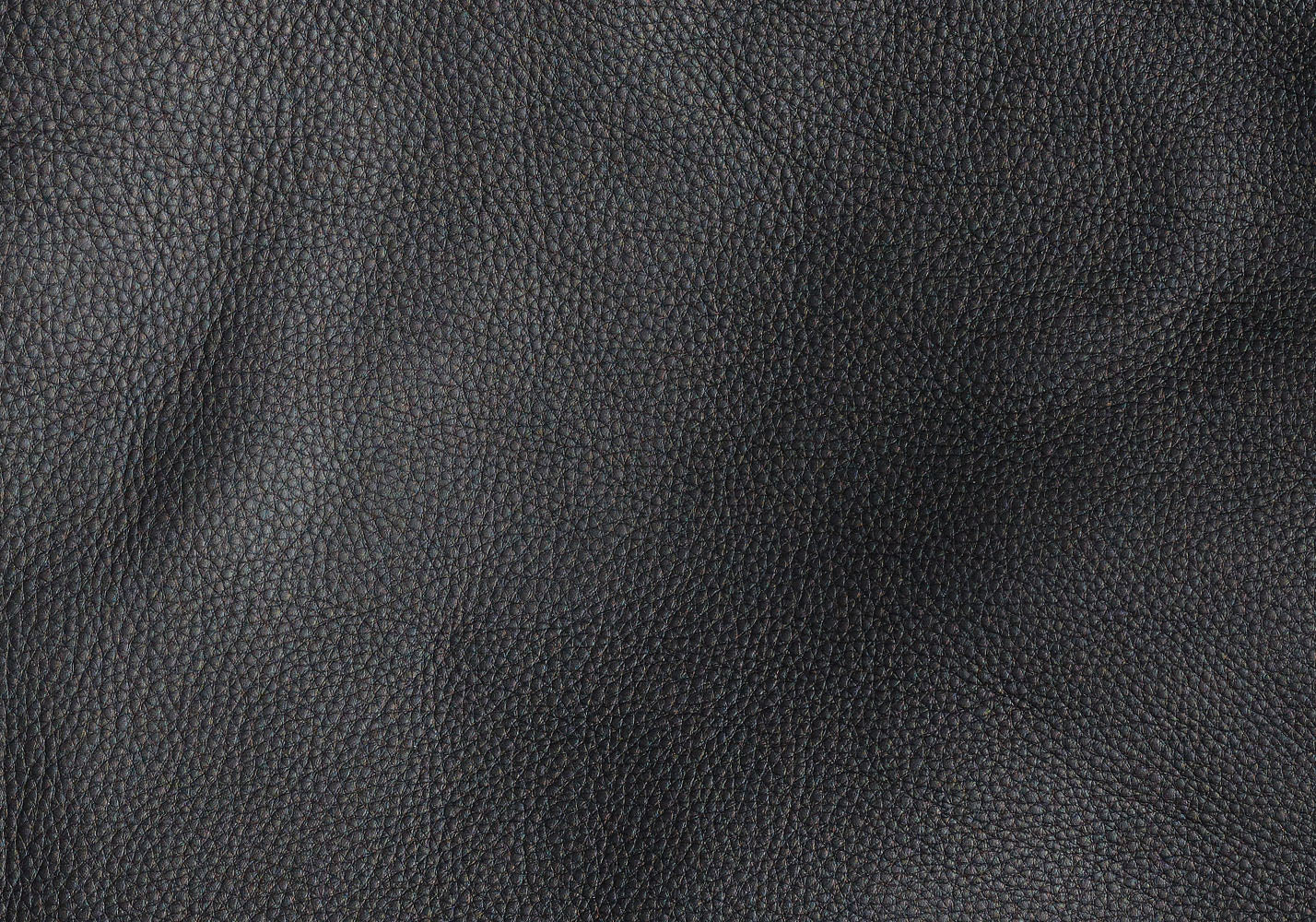
Minkkul
KADOYA has been using it for many years as the official leather of the Japan Motorcycle Sports Association "MFJ official racing suit". It has cleared the "leather inspection test" such as tensile cutting load, tearing load, and abrasion strength at a high level. The raw leather used is domestic Holstein leather, which is characterized by its flexibility even among cowhide. Finished with full chrome tanning, it is soft and easy to adapt to the body while remaining firm. The surface is given top priority to strength, and the pigment sprayed with lacquer is applied to the dyed base.

Vintage Steer
Leather has different textures depending on how it is tanned. Tannin tanning, which uses natural materials, increases its texture the more it is used, and is said to have a "glossy bottom." Chrome tanning, on the other hand, does not have the feel of tannin, but it has high tear strength and is suitable for clothing. In order to achieve both of these, "vintage steer" is chrome tanned, then half of the chromium component is removed, and then tanned with tannin. You can feel the unity that spreads to your body from the first time you wear it, and the suppleness and sitting that leave the tannin-specific waist. It has a tasteful finish that reproduces the ancient teachings of leather to shape the habits of the body.
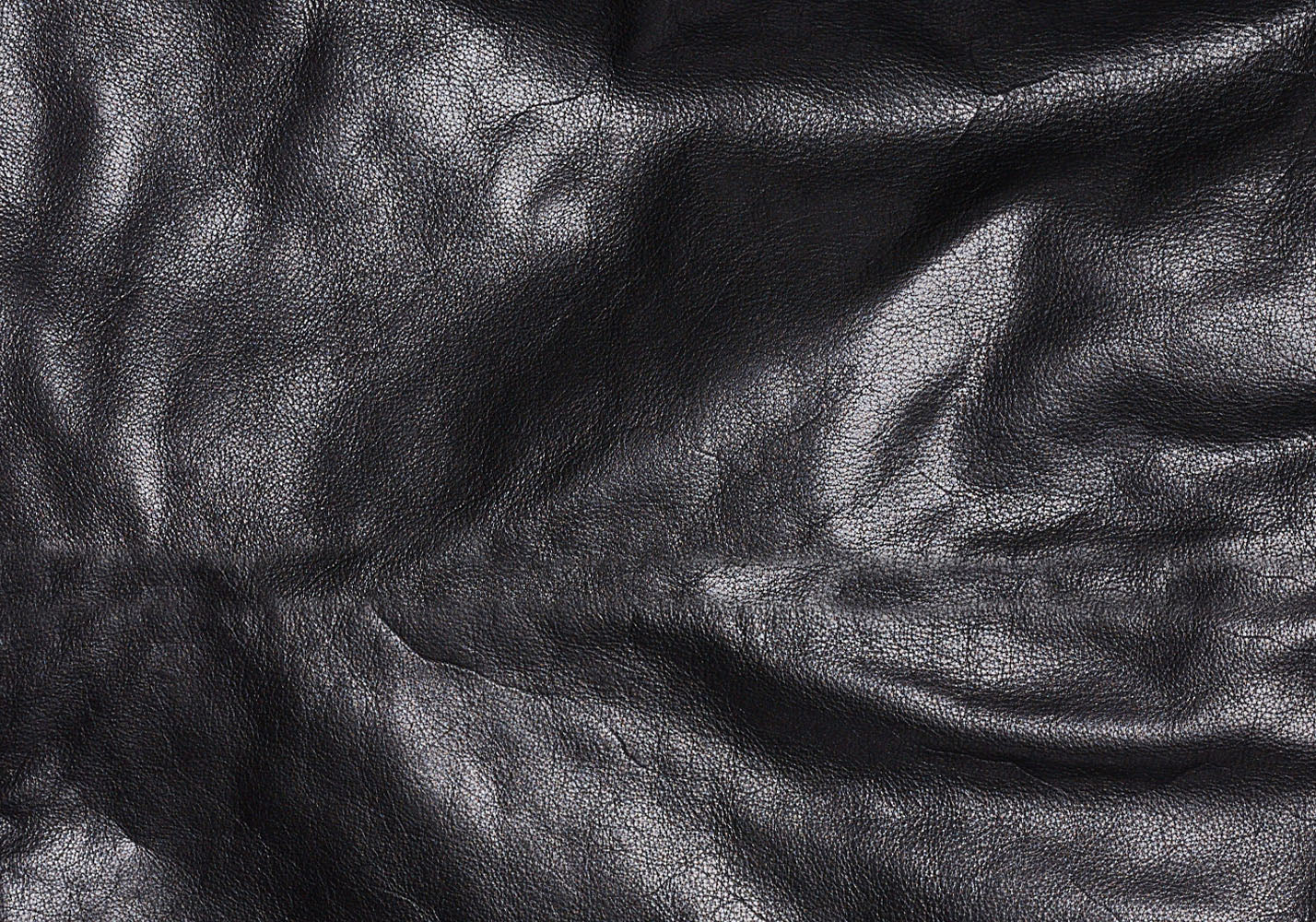
Oil Vintage Steer
The base is combination tanning that contains a lot of natural tannins like the VINTAGE STEER mentioned above. By adding a small amount of chrome tanning agent to the taste of astringent tanned leather that is rich in plasticity, flexibility and physical property fastness are enhanced. In addition, an appropriate amount of oil is permeated, and combined with the aniline dye finish on the surface, it expresses a unique taste with more transparency and smoothness.
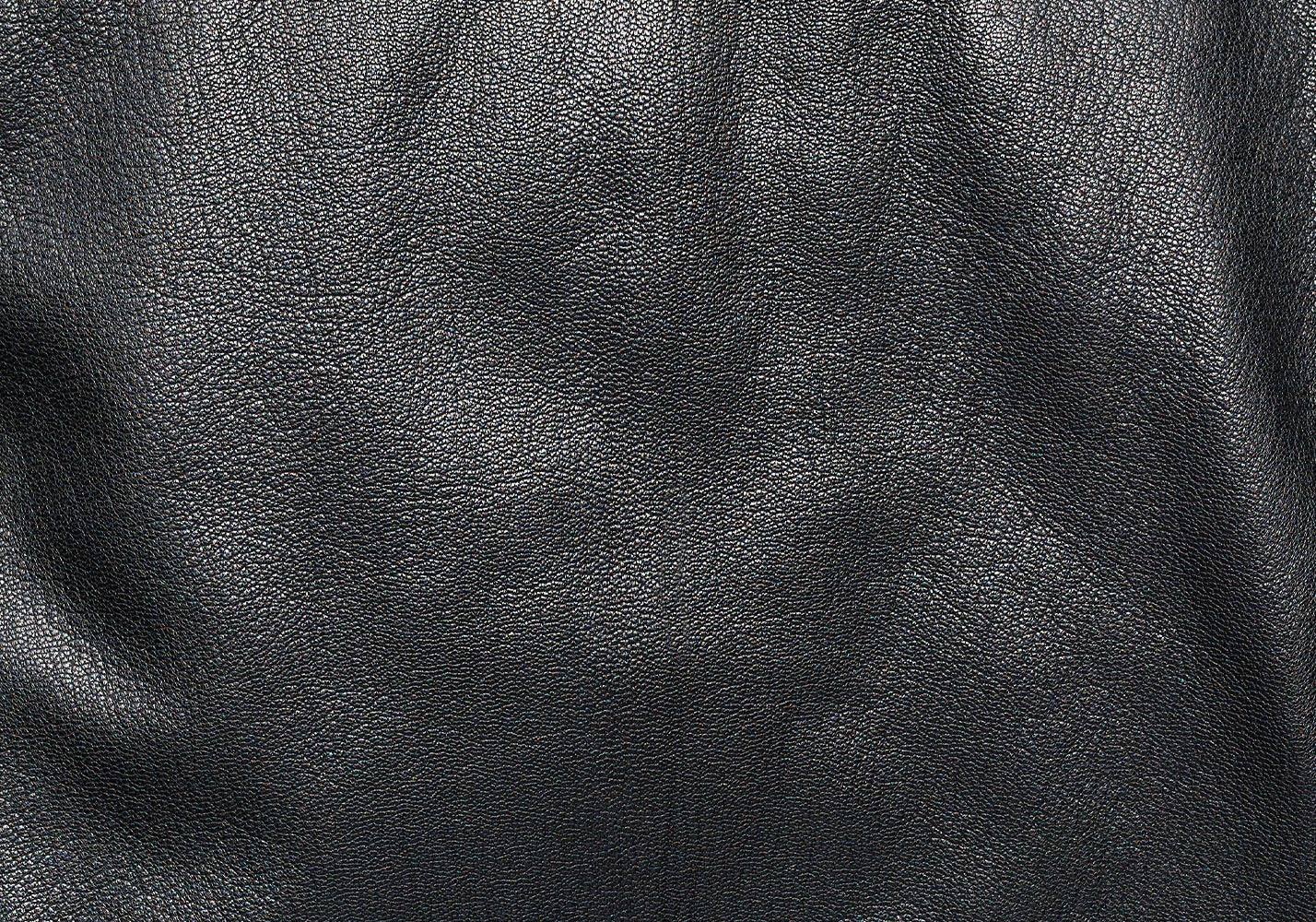
HF-GOAT
Goatskin is tough, lightweight, and has high strength against surface friction. However, the area and thickness of a single piece of raw leather often fall short of the ideal rider's jacket. This issue was cleared in cooperation with partner tanners. A unique embossed feeling is expressed by shrink processing that draws out the characteristics of raw leather and a wild and natural look. Goat skin that is dyed with natural materials and sprayed with the minimum necessary amount of pigment to enhance lightfastness, fading, and fastness to rubbing, while giving it a tenacious and firm feel, making it difficult to feel changes over time on the surface. We are changing the characteristics of this to something more worthwhile to grow.
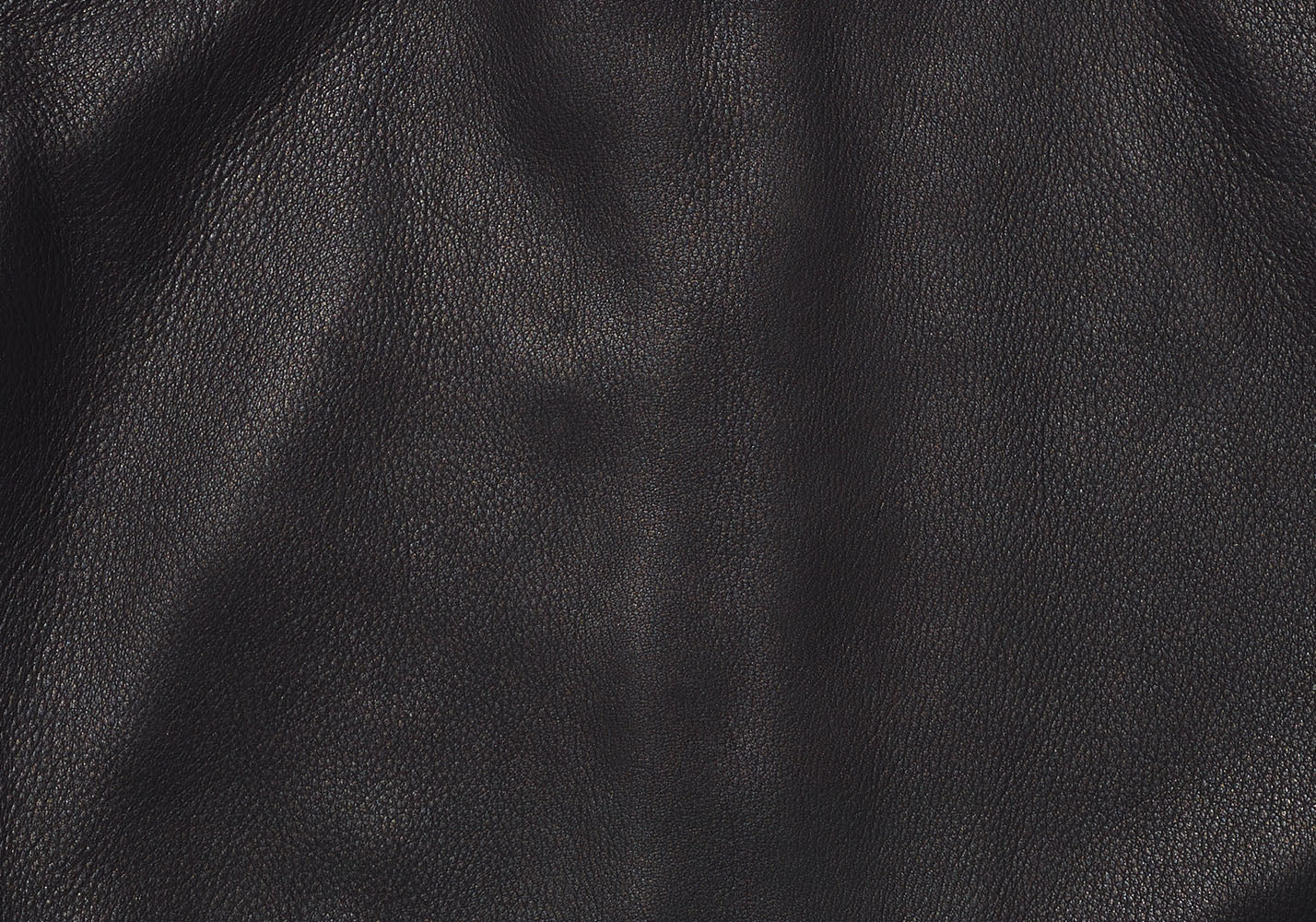
HF-DEER
"Fujioka Yukichi Honten" is dedicated to tanning the natural material "deerskin", skillfully incorporating the colors and tastes of nature, and the traditions and techniques that were born and raised in Nara's beautiful four seasons. ”. Since our founding in 1882, we have valued the know-how of tanning that has been cultivated over generations in a tradition that spans well over 100 years. Always doing forward-looking research. Local water "Utano water" is indispensable for "Fujioka Deer" because climate factors are important for tanning. In addition, in consideration of heat retention and durability, we stick to authentic Spanish drums using African teak wood. The excellent characteristics of deerskin, such as "suppleness", "strength", and "soft texture", can only be realized through careful attention to detail and reliable tanning techniques.
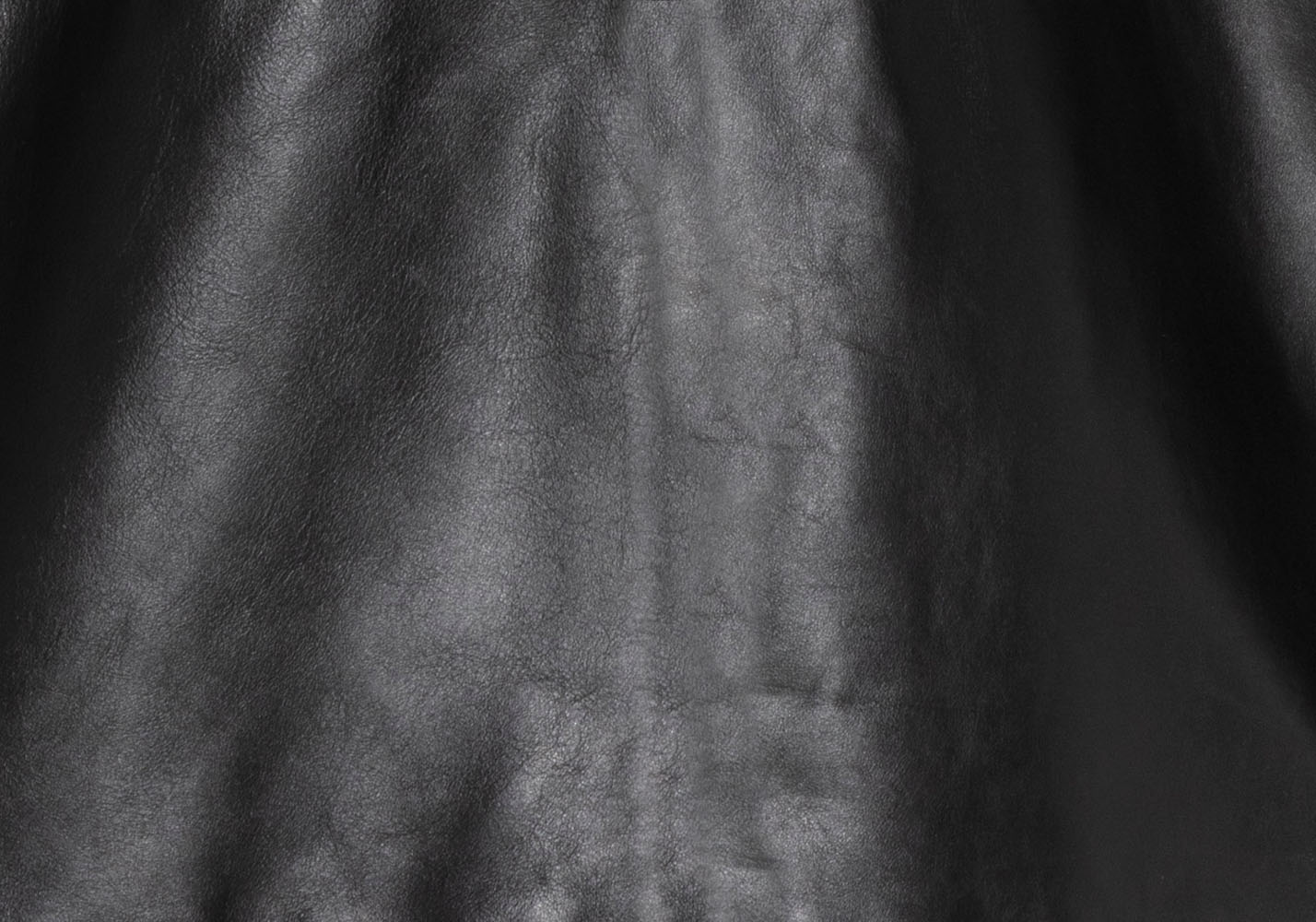
Over Kip
Overkip has a finer surface and more flexibility than steerhide made of mature cowhide. Overkip is a gentle material that is easy to get used to from the first time you wear it. Carefully selected raw leather from North America is tanned with chrome, finished with dyes, and then lightly applied with pigments to create a subdued matte black finish. The luster increases with age, and you can enjoy an elegant contrast.
About
Series
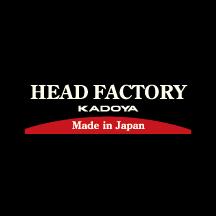
Head Factory
We propose a variety of products based on the unchanging tradition of "each craftsman sewing one garment at a time," the skills and enthusiasm cultivated by Kadoya craftsmen, and the "universal standard model."

MERIDEN
A product group that retains HEAD FACTORY's manufacturing philosophy and incorporates it into an even sharper design. We propose products that coexist with motorcycle leather jackets and street leather jackets.
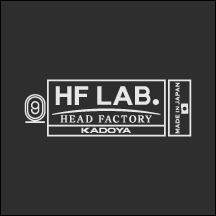
HF Lab.
Confronting various sewing methods and leather. HF's craftsmen have the creativity cultivated through this process. We highlight the individuality of our craftsmen and propose products that are different from conventional HF products.
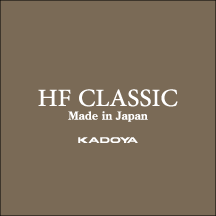
HF Classic
We offer universal clothing that is timeless, and products that are rich in texture, comfortable to wear, and easy to wear on a daily basis, so that the person who picks them up will want to keep wearing them forever.